Services
service
Plastic container manufacturing
Specializing in the production of various types of food plastic containers, the main materials used include PP, PET, PS and PE, and providing the best advice based on product usage.
Customized product development
Conduct professional assessments and tailor unique products based on customers' specific needs to create differentiated value.
Plastic processing technology
Provides a variety of plastic processing methods, including injection molding, pressure molding, vacuum molding and injection blow molding, to meet the design needs of different products.
Service process
Service process
Custom product process
Xinghuacheng has been established for more than 30 years and has rich experience in product design and material properties. It can accurately design and produce products that best meet customer expectations based on customer needs and requirements. We adopt rigorous processes to ensure that we can provide customers with high-quality solutions at every stage.
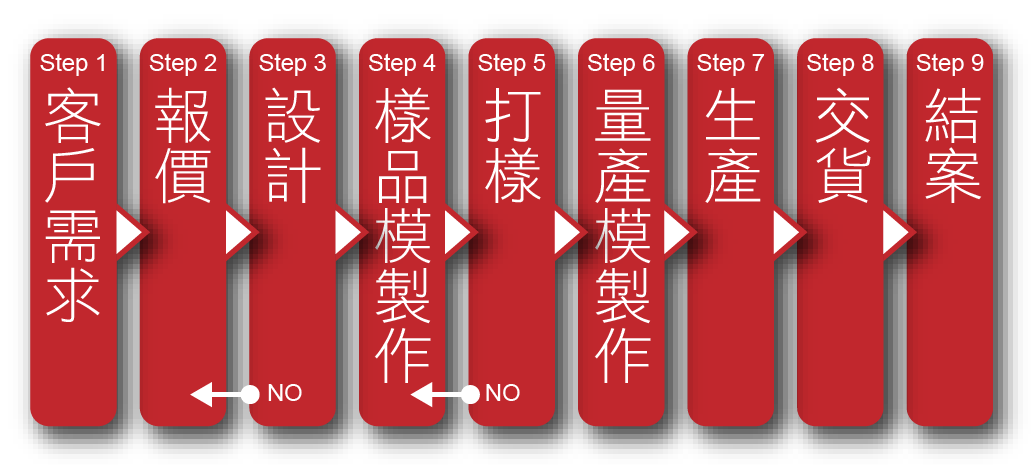
Production process
Judging from the flow chart, most of the production processes of pressure molding and injection molding are the same. Pressure molding has the addition of leather extrusion, and the molding process has different processes.
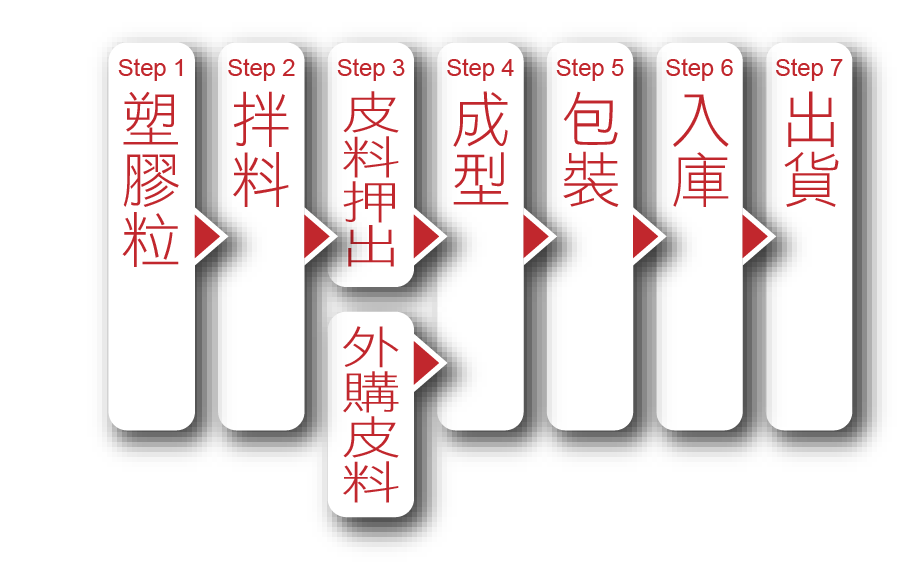
Pressure forming
- Material selection: According to product needs, plastic pellets that meet food regulations are selected. For customized needs, appropriate auxiliary formulas are added to ensure the functionality and safety of the finished product.
- Mixing materials: Mix the plastic granules and auxiliary formula evenly, and decide whether to dry according to the characteristics of the raw materials to ensure a stable texture of the material.
- Leather extrusion: According to product specifications, plastic leather materials with required thickness and width are produced to prepare for molding.
- Molding operation: Put the leather into the molding machine, accurately set the temperature, air pressure, vacuum and cooling parameters according to the product requirements, complete the molding of the entire semi-finished product, and generate the final finished product through processes such as cutting, separating edge materials and stacking.
- Packaging process: Use inner bags to package products to avoid direct contact with the carton, and completely seal the carton with an "H"-shaped seal to prevent foreign matter from entering and ensure product safety.
- Warehousing management: Each carton is labeled with a product label and the production date is clearly marked before placing the product in the appropriate storage area.
- Shipping arrangements: According to customer needs, arrange special vehicles or general logistics vehicles to transport products to ensure that products are delivered safely in the shortest possible time.
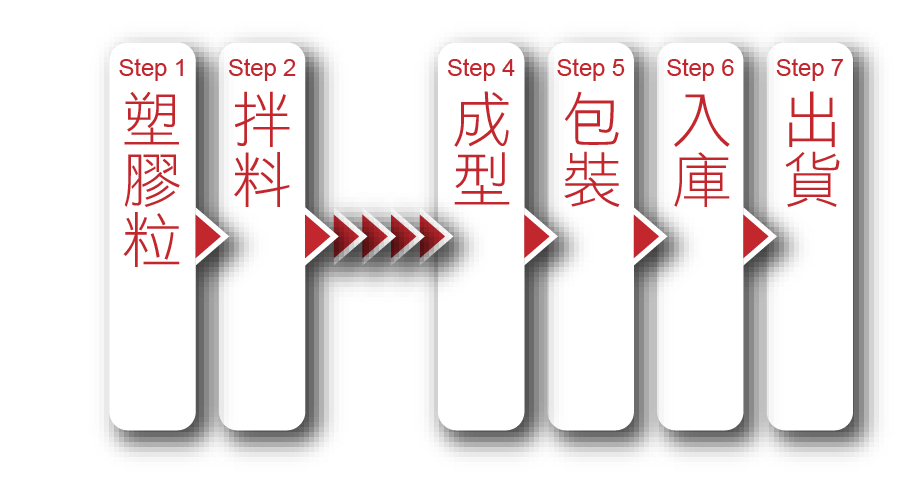
Injection molding
- Melt Injection: The plastic particles are melted and then injected into the mold. Through continuous processes such as mold opening, injection, pressure holding, cooling, and mold opening, the finished product is completed.
- In-film labeling process: If the product requires in-film labeling, the label production and labeling process will be added to ensure that the label is firmly combined with the product to achieve high-quality visual effects.